疲労試験に関する調査
1. はじめに
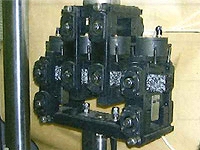
写真-1 疲労試験機の例
『舗装の構造に関する技術基準』では、舗装の必須性能の一つとして疲労破壊輪数が挙げられている。また、『舗装設計施工指針』ではアスファルト舗装の構造設計法として、経験に基づく設計方法と理論的設計方法が示されている。
理論的設計方法においては、アスファルト混合物の弾性係数やポアソン比と定める必要があるが、その測定方法として疲労試験がある。しかし、各機関で保有する試験機のメーカーが異なっていたりする等、測定方法が必ずしも統一されておらず、同一の値が得られるのか不明瞭である等の問題があった。
そこで、TPTでは疲労試験に関し、同一条件で作製した供試体による共通試験及び疲労試験結果に及ぼす影響に関する調査を実施した。
2. 使用試験装置の概要
疲労試験機の構造の一例を図-1に示す。このように、試験機はスパン長の三等分点である4点で支持し拘束することになっており、アクチュエーターによって中央部にある2点の支持点が上下に動き、供試体に曲げひずみを繰返し与える構造になっている。
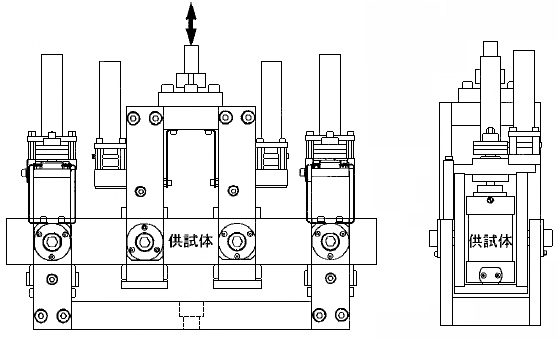
図-1 疲労試験機の構造
3. 共通試験
共通試験の概要
同一条件で作製した供試体を8社に配布して平成15~16年度に疲労試験の共通試験を行った。試験に用いた供試体は、表-1に示すマーシャル性状を有する密粒度アスファルト混合物(最大粒径13mm)とした。供試体は縦型ミキサで製造した混合物をローラコンパクタを用いて締固め度100%を目標にして転圧し、7×30×40cmの寸法の供試体を作製した。この供試体を4面カットして、4×4×40cmの寸法に整形したものを用いた。供試体は、作製機関の違いが試験結果へ影響を及ぼすことを排除するため、同一機関で作製し、同一機関で切断した。切断した供試体は、各機関へ配布する際に密度が偏らないように配慮した。
年度ごとに検討した内容は以下のとおりである。
- 平成15年度
- 試験機の作動精度
- 供試体養生時間
- 試験中の供試体温度の変化
- 供試体の拘束力の影響
- 供試体の拘束間隔の影響
- 供試体の拘束長さの影響
- 平成16年度
- 試験時の発生応力
- 試験結果の整理方法の影響
- データの選別方法
- 試験条件統一の効果
表-1 使用混合物の配合とマーシャル性状 | |||||||||||||||||||||||||||||||
|
共通試験により得られた結果
- 平成15年度
- 試験機の作動精度は試験結果に影響を及ぼすため、事前にキャリブレーションを行い、設定ひずみと供試体中央部のひずみの関係を把握し、供試体中央部に所定のひずみを与えるよう設定ひずみを補正する必要がある。
- 供試体の養生時間は、空冷式と水冷式で異なる。空冷式の場合、試験温度に保った養生槽で2時間程度(図-2(a))、試験槽にセッティングし構内の温度が試験温度に回復してから1時間程度養生するとよい(図-3)。水冷式の場合、試験槽にセッティングしてから30分程度養生するとよい(図-2(b))。
- 空冷式試験槽で200μを超えるひずみを与え疲労試験を行う場合、供試体発熱の影響の考慮を要する(図-4(a))。水冷式試験槽を用いる場合、供試体に与えるひずみが400μ以下であれば、発熱の影響はない(図-4(b))。
- 供試体の拘束力は試験結果にあまり影響せず、本検討の実験条件である196N(20kgf)から1471N(150kgf)の範囲であれば問題ない。
- 供試体の拘束時間は、拘束治具の緩みを考慮すれば、供試体の拘束間隔は短時間であるほどよく、10分程度未満、できれば自動締付けによる1分以下が望ましい。したがって、拘束間隔と2.で得られた養生時間を併せて考慮すると、空冷式試験槽と手動式供試体締付け機構を組み合わせた試験機は、供試体を再拘束するため試験槽の扉を開けると槽内温度が変化し供試体の温度が変化することになるため、あまり望ましくない。
- 供試体の拘束長さは破壊回数にあまり影響を与えないが、供試体中央部で破壊を生じさせるため、供試体拘束長を5.5cmにすることが望ましい。
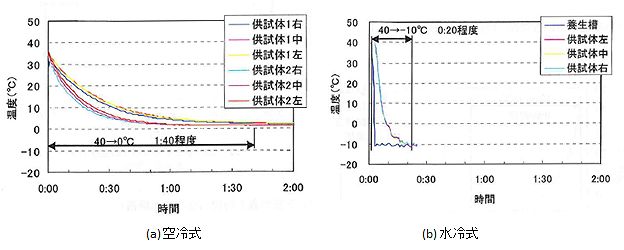
図-2 養生中の供試体の温度変化
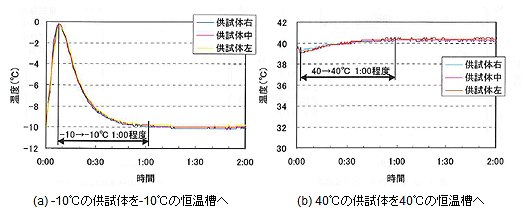
図-3 試験装置に設置後の供試体の温度変化(空冷式)
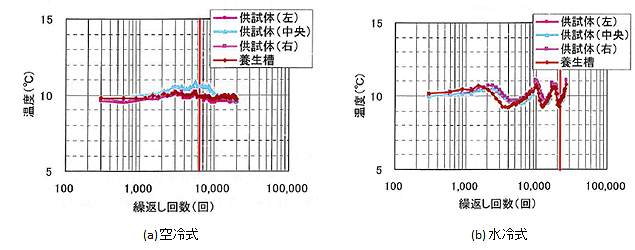
図-4 繰り返し回数と供試体温度
- 平成16年度
- 載荷時に生じる発生応力は、同一ひずみの場合でも試験実施機関によって異なり、これが機関間で疲労破壊回数がばらつく一因と考えられる。機関間で発生応力が異なるのは、試験機の差であり、特に供試体拘束治具の構造や選びによるものと考えられる。発生応力の機関内誤差は、ひずみの増加によって大きくなる傾向があるが、共通試験を実施した1機関を除けばあまり大きくない。
- 載荷回数-応力曲線から疲労破壊回数を求める際の接線の描き方は機関によって異なる。疲労試験方法の統一のため、載荷200回以降を有効データとし、最小2乗法により2本の対数直線を描き、交点を計算して疲労回数を求める方法を示し、この方法で整理方法を統一したが、各機関独自の方法で整理した疲労破壊回数路とあまり変わらず、結果にほとんど影響しないことが明らかになった(図-5)。
- ひび割れ発生箇所が破壊回数のばらつきに影響を及ぼし、供試体中央位置から±2cm程度の範囲内にある試験データを抽出したが、機関間の試験誤差が収束する傾向があることが明らかになった。
- 共通試験のデータを統計的に検討した結果、疲労破壊回数の全体誤差に占める機関内誤差の割合は一部を除き10%以下であることが明らかになった。また、発生応力の全体誤差に占める機関内誤差の割合は10%以下であり、変動係数は機関内比較と機関間比較ともに概ね10%以下であることが明らかになった。
- 試験方法とデータ整理方法の統一は、機関間に生じる疲労破壊回数の誤差の収束に有効であることが明らかになった(図-6)。
- 前年度までの検討から、得られた結論も考慮し、試験方法を確立することができた。
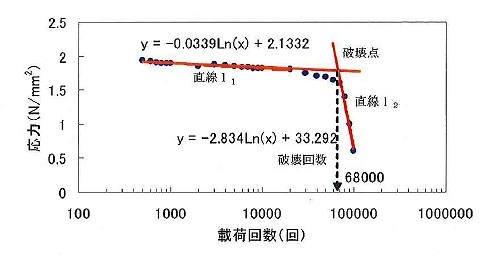
図-5 試験データから破壊点を定める共通整理方法
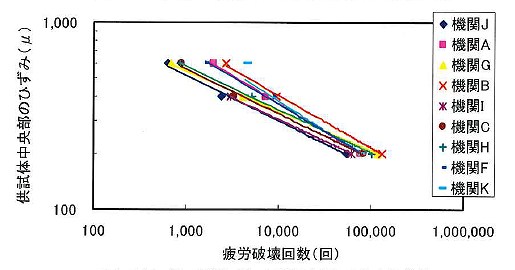
図-6 統一試験・データ整理方法による疲労曲線
4. 研究成果の反映先
本研究の成果は日本道路協会『舗装調査・試験法便覧』(平成19年6月)に反映されている。